How Steel Corrodes?
- chanhonkit
- May 15, 2022
- 5 min read
Updated: May 16, 2022
Corrosion is deterioration of metal by a electrochemical process. Corrosion is present whenever there are two dissimilar metals or steel within the same structure, an electrolyte or water with any type of salts dissolved in it and a conductive path between the dissimilar metals.

When iron particles have been exposed to oxygen and moisture, rust begins to form.
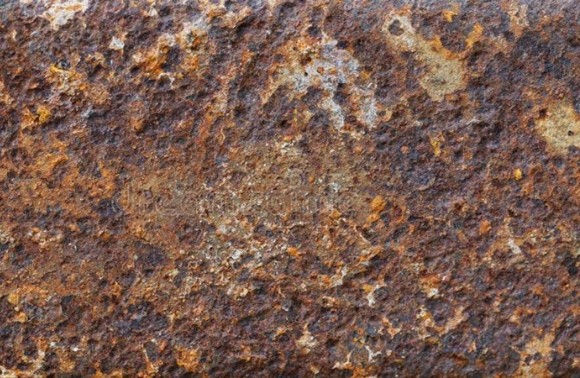
The iron particles are then oxidized, forming Fe2+. When Fe2+ is formed, 4e- are released and the free electrons are transferred to less active sites, then oxygen is converted to oxygen ion.
Recombining of these ions produce an iron-corrosion product ferrous hydroxide.

This reaction is commonly known as current flow from anode (more active site) to the cathode. (less active site).
Any metal structure exposed to the environment will corrode over time. Rate of corrosion depends on the environment the metal is in. Since atmospheric corrosion is so widespread, it is recommended to take effective precautionary measures when it comes to corrosion prevention.
Corrosion can be controlled through painting, cathodic protection, galvanizing, or tape wrapping (pipe piles) or combination.
Concept of Cathodic Protection: Anode, Cathode, and Electrolyte Galvanic Cell

Corrosion deteriorates the steel causing a lot of money to replace or retrofit. Cathodic protection is one of the options to control corrosion.
It is a technique used to control the corrosion of a metal surface by making it the cathode (less active site). A simple method of protection connects the metal to be protected to a more easily corroded "sacrificial metal" or to act as the anode (more active site).
If two dissimilar metals are connected, there will be a galvanic cell formed where the more anodic/less noble material oxidizes/corrodes away. The common anode materials for cathodic protection are Aluminum, Zinc and Magnesium.
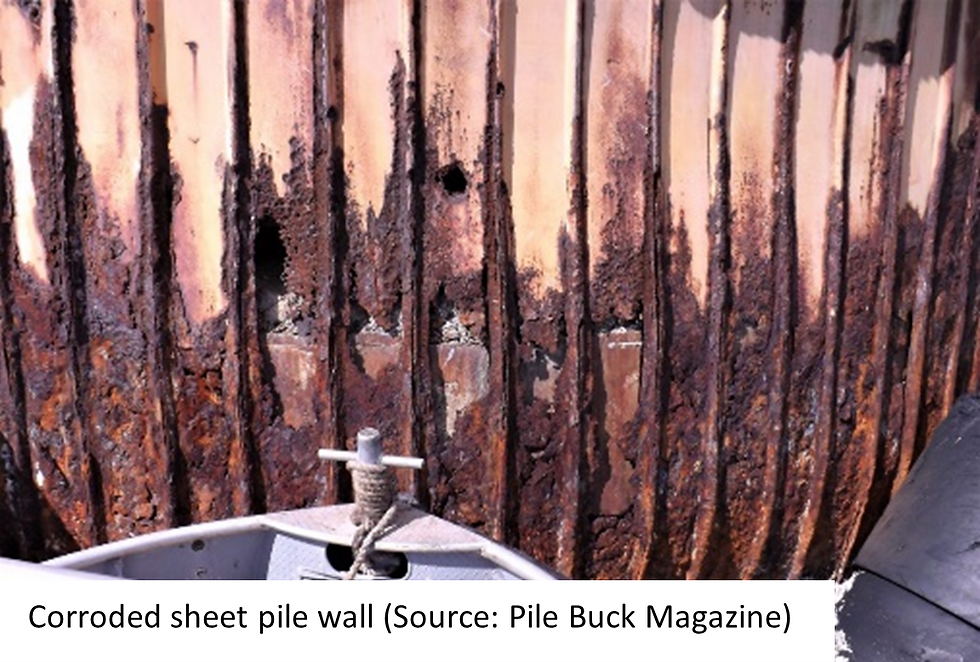
Cathodic Protection (CP) increases the design life and can be replaced much more easily than reapplication of corrosion protection coatings. It may need or may not be need electric power.
It can be utilized in conjunction with corrosion coatings to form a complete corrosion protection system. However, it cannot be used to prevent atmospheric corrosion.
Cathodic protection can protect structures such as pipes, above ground storage tank bases, buried tanks, vessels, condensers, well casings, steel piles, ship, and even marine structures such as jetty, wharf, harbor, pier, and platforms.
In designing anodes, environmental factors that needs to be considered are the design life of the system, coating thickness (if any), surface are to be protected, degradation of coating in the ground, coating degradation rate, salinity, seawater resistivity, highly/poorly aerated waters, tidal flow rate and temperature. Moreover, the designer should also consider the anode electrochemical capacity (Ah/kg), standoff of anode, anode mass and dimension.
Total anode current can be determined from the area of the structure when appropriate current density has been decided.
Other Corrosion Protection Options: Paint, Galvanizing and Tape Wrap
Aside from cathodic protection, other corrosion protection for steel includes paint, galvanizing and tape wrap.
Painting is the most popular corrosion protection application method because it is cheapest and easiest ways to prevent corrosion. Impervious and sufficient thick paint can prevent the ions from entering the metal surface, reducing the chances of formation of rust. Additives such as phosphates and borates are used as corrosion protection pigments form layers of protection at the anode site. Painting can be used in conjunction with cathodic protection coatings to form a complete corrosion protection system. Epoxy, urethane and polyurethane are the common passive corrosion paints.
Galvanizing is application of zinc coating to protect the steel or iron to prevent rusting. Zinc coating can be applied thru electroplating, mechanical plating, sherardising, continuously galvanized wire or sheet, metal spraying or the general hot dip galvanizing. Unlike painting, galvanizing cannot be done on site because it requires large equipment. Exposure to harsh environment can speed up the zinc damage, needing frequent maintenance check-ups. Galvanizing can be chipped and peeled so application should be done properly.
Tape wrap is another corrosion protection typically applicable to pipes. Tape wrap like petrolatum/wax/grease tape can be used on dry, wet and submerged water even without primer. It provides long term protection to pipes, piles, flanges, valves and have a service temperature up to 230°F (110°C). Polyethylene tape coat is another option of tape wrap but this requires a primer coat and multiple layers of polyethylene tape.
Impressed Current (ICCP) vs Galvanic Cathodic Protection
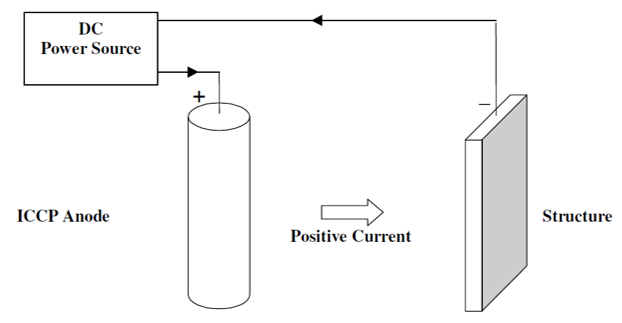
The main difference between Impressed Current Cathodic Protection (ICCP) and Galvanic cathodic protection is ICCP is connected to an external power source or a DC power supply so it can drive the electrochemical reaction for metal to be protected.
Transformer-rectifier connected to AC Power can also be used when DC is not available. ICCP are commonly used in structures where protection requirements are high. It can be adjusted and monitored based on current conditions.
Since it uses an external power source, it needs lesser number of anodes compared to galvanic cathodic protection. It is important to check all connections have integrity of insulation to avoid damage to the structure and other structures.

On the other hand, galvanic anodes are independent of any external power source. It is used to protect well-coated areas where requirement based on water or soil resistivity is lower. It can also be used in smaller surface areas like sheet pile wall system.
It is easier to install and can be connected directly to the structure. Galvanic anodes are self-adjusting. Proper material selection ensures no overprotection and coating damage. Unlike ICCP, incorrect connections will not damage neighboring structures.
Galvanic Anodes: Magnesium, Aluminum, Zinc

The 3 main types of anode material are Aluminum (Al), Magnesium (Mg) and Zinc (Zn). These materials are more anodic/less noble thus corrodes away and protect the steel.
Among the three materials, Magnesium is most negative electro potential and best used on shore pipelines where resistivity is higher. It is either supplied as ribbon or rod-type and are only suitable for use in soils and freshwater.
Zinc and aluminum, on the other hand, are used in salt water, where the resistivity is generally lower. Zinc used to be the traditional anode material but later replaced by Aluminum because Zinc, with its cadmium activator is harmful to the marine environment.
Moreover, Aluminum is lighter, can protect large areas at a small amount and higher driving voltage than Zinc. Aluminum is also the only material that can be used in brackish water. Aluminum anodes are used commonly in sheet pile wall systems while zinc anodes are used in ship hulls.
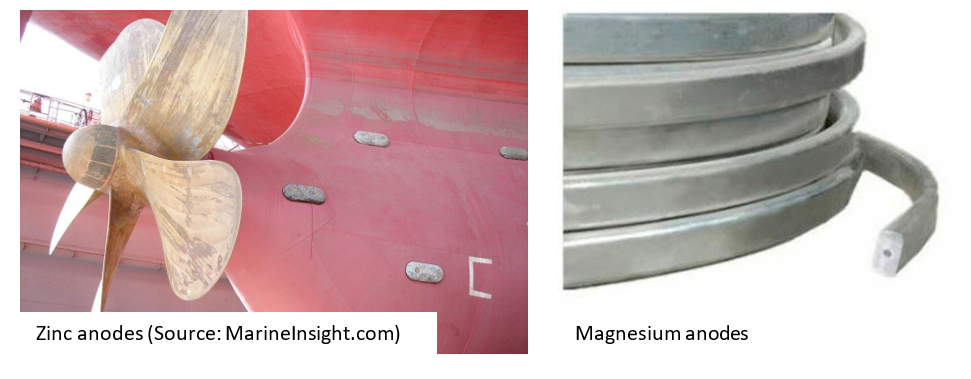
Relevant Standards
Cathodic Protection Systems:
• DNV RP B401 Cathodic Protection Design Rules & Standards
• BS EN 13174 Cathodic Protection of Harbour Installations
• Other sources:
• NACE RP 0176
• NACE RP 0386
• NORSOK M503
• BS EN 12473, 12495, 13173
Installation, Commissioning and Maintenance
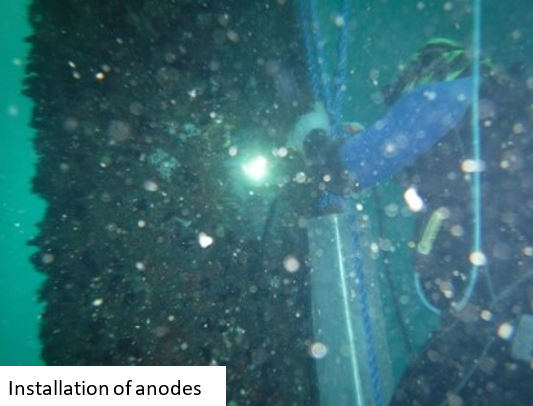
Typical connection of stand-off anodes on sheet and pipe piles are bolted or welded. For welded type, the installer or the client usually suggests the wet weld method to use.
Commissioning and Maintenance includes:
· Pre-commissioning survey
· Commissioning survey
· Post-commissioning survey
· Annual potential survey
· Post installation visual inspection
· Rectification instruction

Commissioning survey is being conducted before and after installation to check the structure to electrolyte potential. Post installation visual inspection is done to check the physical condition of the anodes.
Dimensions of anodes and corrosion condition of structure is being checked to ensure that the anodes are not under protected or overprotected. Otherwise, calculation must be revisited, and necessary rectification should be done.
At ESC, we will help you find the right corrosion protection system solutions for your project. Get what you need to protect your steel today!
Email us ✉️ zulfan@escpile.com or 📞 +62 811 980 376